Finest Practices for Effective Tank Welding Inspection Processes
Wiki Article
The Crucial Function of Tank Welding Evaluation in Ensuring Structural Honesty and Safety And Security Compliance in Industrial Applications
In the realm of commercial applications, storage tank welding inspection emerges as a pivotal aspect in safeguarding structural honesty and guaranteeing conformity with security regulations. Using a combination of methods such as visual evaluations and advanced screening approaches, these examinations serve to determine and mitigate possible defects before they rise into substantial risks. The effects of these methods extend past simple governing adherence; they basically influence operational effectiveness and possession longevity. Nonetheless, the complexities surrounding the examination procedure trigger a closer examination of its techniques and outcomes, exposing layers of significance that value further expedition.Relevance of Storage Tank Welding Evaluation
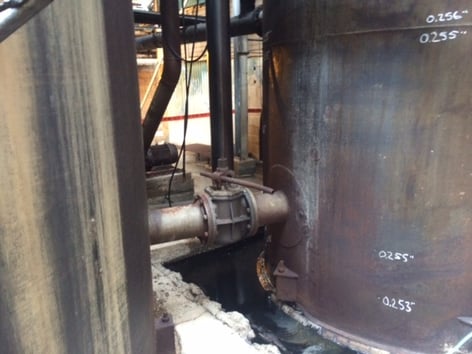
Guaranteeing conformity with sector requirements and laws is another considerable element of tank welding assessment. Regulatory bodies mandate stringent guidelines for the construction and upkeep of tank, and thorough examinations assist organizations abide by these needs. Non-compliance can lead to severe fines, including penalties and closures, even more stressing the requirement for strenuous inspection protocols.
Additionally, storage tank welding inspection plays an important function in keeping operational effectiveness. In recap, the importance of container welding examination exists in its capacity to safeguard public wellness, secure the setting, and make certain conformity with regulatory frameworks.
Secret Assessment Techniques
Reliable storage tank welding evaluation relies upon a selection of crucial strategies that make sure extensive examination of weld top quality and architectural honesty. Amongst one of the most common methods are aesthetic evaluation, ultrasonic screening, radiographic screening, and magnetic particle screening - Tank Welding Inspection. Each technique offers distinct benefits in analyzing various aspects of the weld
Visual examination offers as the first line of defense, enabling examiners to recognize surface problems, irregularities, or incongruities in the weld grain. Ultrasonic screening employs high-frequency sound waves to identify interior problems, such as fractures or voids, supplying a thorough assessment of weld integrity. This method is particularly reliable in discovering issues that might not be visible on the surface.
Radiographic testing makes use of X-rays or gamma rays to create pictures of the welds, exposing interior stoppages and providing a permanent document for future reference. This strategy is very effective for essential applications where the risk of failure must be lessened.
Lastly, magnetic bit screening is utilized to identify surface and near-surface defects in ferromagnetic products. By applying magnetic areas and great iron fragments, examiners can determine stoppages that might jeopardize the architectural stability of the container. Together, these strategies develop a robust structure for making certain top quality welds in commercial applications.
Compliance With Security Requirements

Normal inspections play a crucial role in making certain conformity by identifying potential failures or deviations from recommended criteria. Inspectors are educated to review weld high quality, verify material specifications, and assess the general structural honesty of storage tanks. Their proficiency is vital in ensuring that welding procedures meet the called for safety requirements.
Furthermore, compliance with security criteria not only shields workers find out here now but additionally safeguards the setting from potential risks such as leaks or tragic failures. Organizations that prioritize safety conformity are better placed to reduce threats, improve operational efficiency, and foster a culture of safety within their workforce. In recap, keeping strenuous conformity with safety and security requirements is essential for the effective operation of tank welding activities in commercial setups.
Benefits of Normal Assessments
Routine evaluations are important to maintaining the structural honesty and safety of bonded containers. These assessments provide i loved this a methodical approach to recognizing possible defects or weak points in the welds, guaranteeing that any type of issues are addressed before they rise into considerable failures. By performing normal evaluations, organizations can find rust, tiredness, and other forms of wear and tear that may jeopardize tank performance.In addition, consistent inspections add to compliance with sector policies and criteria. Sticking to these standards not just mitigates legal threats however also improves the organization's online reputation for safety and security and dependability. Regular inspections foster an aggressive security culture, encouraging employees to identify and prioritize the value of equipment honesty.

Instance Researches and Real-World Applications
Case research studies and real-world applications highlight the tangible effect of reliable container welding assessment methods. Complying with the implementation of rigorous welding inspection procedures, including visual and ultrasonic screening, the facility determined important imperfections in weld joints that can have led to devastating failings.Likewise, a water treatment plant executed a thorough assessment program for its storage tank welding procedures - Tank Welding Inspection. By integrating non-destructive screening techniques, the plant had the ability to identify very early indicators of corrosion and exhaustion Bonuses in weld joints. This timely treatment extended the life expectancy of the containers and guaranteed compliance with safety and security policies, hence guarding public health
These study highlight the importance of routine and organized tank welding evaluations. By focusing on these methods, sectors can minimize risks, enhance architectural stability, and make sure conformity with security requirements, ultimately resulting in boosted functional performance and reduced liabilities.

Conclusion
In conclusion, container welding evaluation is a crucial element of preserving architectural honesty and safety in industrial applications. Using different evaluation methods makes sure early detection of prospective flaws, thereby preventing devastating failures.Report this wiki page